ANNEXURE 9: |
Handling of occupational hygiene personal sampling with regards to COVID-19 |
(For Information purposes)
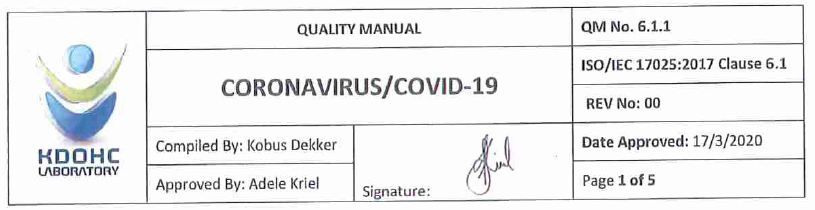
This document outlines and addresses the preventative measures for the Coronavirus/COVID19. This document will specify the preventative measures and the care to be taken when handling, preparing, issuing, retrieving and decontaminating sampling equipment for KDOHC.
It is the policy of KDOHC to ensure all the activities underlined in this procedure be performed and are undertaken to ensure health and safety of all KDOHC employees, clients and service providers and suppliers. Note that the specifications in this procedure should be seen as a minimum requirement only.
https://youtu.be/JKpVMivbTfg
Parliament Highlights. Gan Kim Yong speech
Centres for Disease Control and Prevention. CDC 24/7: Saving Lives. Protecting People
https://www.cdc.gov/coronavirus/2019-ncov
4. |
DEFINITIONS AND ABBREVIATIONS |
Decontamination solution - Solution of Bleach/bleach and water (20ml Bleach per one litre of water)
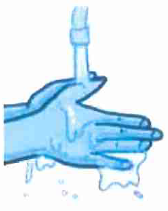
Issuing of equipment will be done in accordance with company policies and procedures, with the following recommendations:
• |
Always assume that equipment is contaminated |
• |
Receive equipment box from the laboratory |
• |
Fit re-useable, impervious gloves (it may be necessary to remove all jewellery and watches) |
• |
Take equipment out of the equipment box |
• |
Close the equipment box as soon as possible after removing the equipment |
• |
Wipe all the equipment with a decontamination solution consisting of a Bleach and water solution |
• |
Conduct calibrations and sample assembly as per normal with your gloves still on |
• |
Before approaching employee to issue sampling equipment fit your mask and goggles to protect your T-zone (figure below) |
• |
Return to the office and decontaminate your re-usable gloves before taking it off |
• |
After decontamination, take it off and let it dry |
• |
REPEAT THE PROCESS WHEN RETRIEVING EQUIPMENT |
• |
When back at the office after retrieving of equipment, place all noise dosimeters inside a Ziplock bag, seal and put it in the equipment transport box |
• |
If dosimeters stay on the site, decontaminate (wipe) with a cloth soaked in decontamination solution and submerge the windshield in the decontamination solution |
• |
Wipe the sampling pumps and the rest of the equipment with a cloth soaked in decontamination solution |
• |
Decontaminate the outside of the equipment transport box |
T-zone
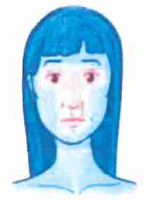
5.2 |
Collecting equipment transport box from sites |
• |
Always assume that equipment is contaminated |
• |
Fit re-useable,impervious gloves (it may be necessary to remove all jewellery and watches) |
• |
If noise dosimeters are not contained inside Ziplock bags OR when cyclone grid pots are not fitted to the cyclone anymore, assume the entire box is contaminated inside and seal the box immediately with a cable tie |
• |
Mark the equipment box with a special sticker indicating that the content should be considered as potentially contaminated |
• |
Inform the client that the box is potentially contaminated and that they should put the box in quarantine for a period of 14 days |
• |
Take of your gloves and put it in a refuse bag, seal and transport it back to the laboratory |
• |
If satisfied, take the box and put in the refuse bag with the contaminated gloves to return to the laboratory |
5.3 |
Decontamination and unpacking of equipment transport boxes at the laboratory |
Outside decontamination
• |
Receive the equipment transport boxes at a table outside the lab |
• |
Fit a clean pair of gloves and goggles |
• |
Take out the equipment transport box and wipe it with decontamination solution |
• |
Submerge the contaminated gloves and Ziplock bags into the decontamination solution and hang out to dry |
• |
Wipe all the equipment with decontamination solution and put it on a transport tray |
• |
Spray the equipment box inserts (sponges) with decontamination solution |
Inside decontamination
• |
Take sample equipment into the lab on the transport tray |
• |
Take equipment to Wet lab for post calibration checks |
• |
Fit a clean pair of gloves |
• |
Remove the cyclone and grid pot from the sample cassette and submerge both in the decontamination solution |
• |
Place the cyclone and the grid pot now into the ultrasonic both for further cleaning |
• |
Disassemble the sample cassette by firstly removing the Top inlet and Extension sections of the cassette |
• |
Take the filter with the mentioned two sections of the cassette to the weighing facility |
• |
Remove your gloves and submerge the contaminated gloves into the decontamination solution and hang out to dry |
• |
Take the filter out of the cassette and place it in a petri dish |
• |
Take the sampling cassette back to the wet laboratory and submerge in the decontamination solution before placing it in the ultrasonic bath for further cleaning |
• |
When the pumps are dry, return to the charging docking stations |
5.4 |
Decontamination of noise dosimeters |
• |
Remove the windshield and submerge in decontamination solution |
• |
Place in the fume extraction hood and allow to dry |
• |
Wipe noise dosimeters with decontamination solution |
• |
Wipe down transport trays |
• |
Remove your gloves before moving equipment |
• |
When preparing equipment to be transported to the client, consider all equipment, originated from laboratory, to be decontaminated |
• |
All working surfaces in the laboratory will be wiped down at the end of each shift |
• |
Laboratory personal to wear gloves when working with control cards |
• |
Issuers of equipment on the sites need to wear gloves when handling/completing control cards |
5.6 |
Decontamination of Office environment |
Decontaminate the following items in the office environment by one dedicated person per day:
• |
All doorknobs and handles |
• |
Keyboards, mouse, printer control panel and telephones |
• |
Door remote, alarm control pad |
• |
Tabletops (all working surfaces), Kettle, microwave, fridge |
• |
All utensils, cups, glasses,plates etc. to be washed after use with soap and water |
• |
Designated cutlery and crockery to be provided for each employee |
• |
Only paper towels to be allowed in the bathrooms and kitchen. |
• |
All company vehicles to be cleaned by KDOHC employees once a week (no external cleaning companies to be used) |
• |
Vehicles to be disinfected on the inside on a daily basis |
• |
Visitors to sign register |
• |
Visitors to disinfect hands on arrival |
• |
A poster will be displayed on the front door stating that if you experience any symptoms of the Corona/COVID-19 virus, please refrain from entering. Consult your doctor |
• |
When suspecting that an office employee is sick or symptomatic, make the laboratory manager aware and get suspected employee to seek medical advice |
All records are kept as per QM No. 8.4/F-01.